Quality and Productivity Improvement for Enterprise Competitiveness (Basic KAIZEN) (A)
new!
Diligent Study in a Cycle of Lectures (Mental Study)‚ Practical Work (Hands-on Study) and Evaluation
Oct.8 to Oct.16‚ 2024 (Remote Training)‚ Oct.21 to Nov.20‚ 2024 (Training in Japan)
Hisatoshi TORIKAI‚ Course Leader
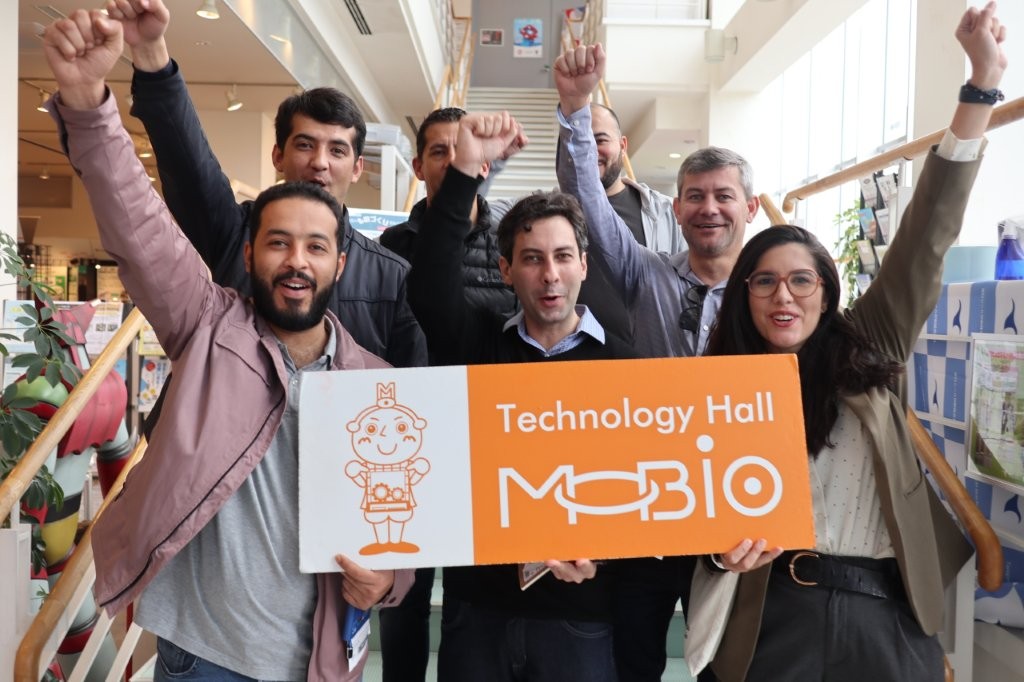
Visit to MOBIO (Monodzukuri Business Information-Center Osaka)
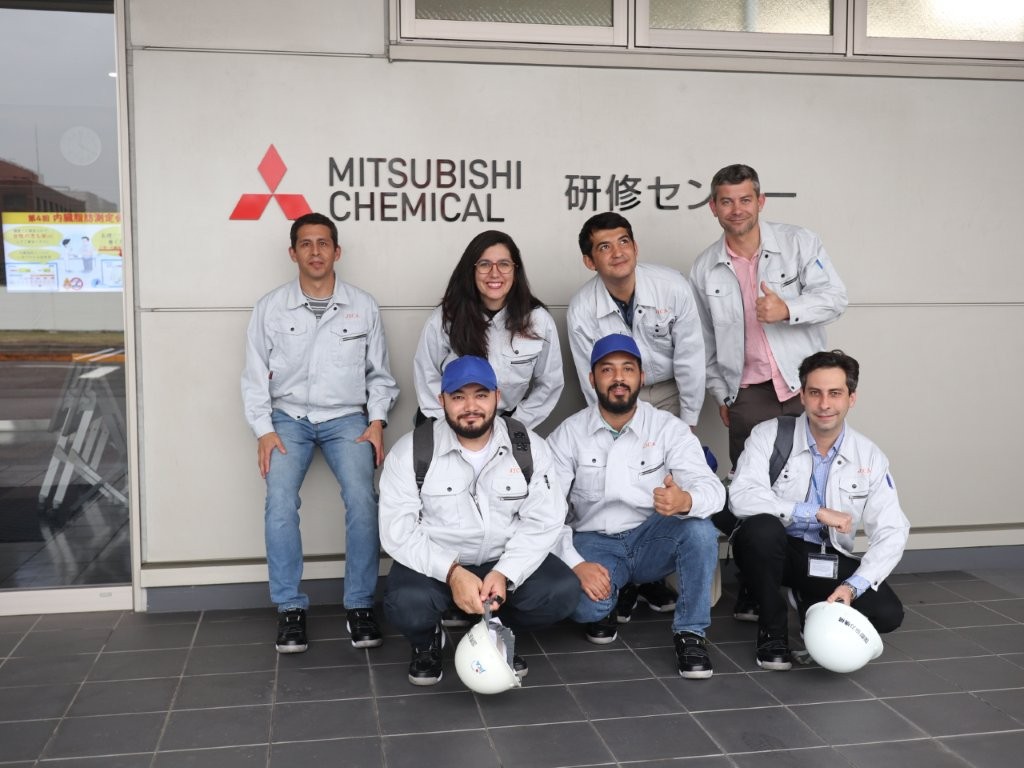
Visit to Training Center of Mitsubishi Chemical Group‚ Kyushu Plant
In the preliminary remote training‚ the trainees clarified their respective issues and brainstormed solutions for them with their colleagues‚ and then brought the results of that brainstorming to Japan. During the remote training‚ trainees who had participated in this course previously also gave presentations of their action plans‚ so the new batch of participants seemed to have acquired an image of what an action plan should be like. In addition‚ I was able to follow up on the fact that the previous batch of participants were upgrading their action plans to the implementation stage.
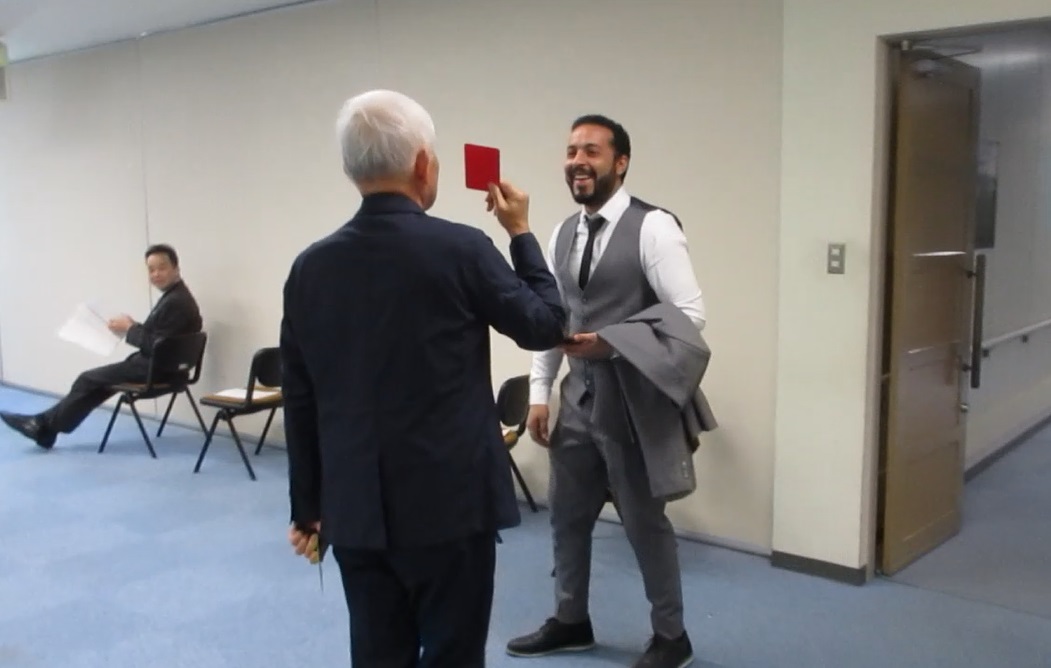
A Trainee being shown a Red Card due to Late Arrival
As a gmonozukuri team‚h the participants took gdeadlines are importanth as their motto‚ and resolved to be punctual. The penalty for unpunctuality was to perform a dance or song at the party held after the closing ceremony at the end of the course. However‚ seeing them volunteer for the penalty (?) and perform a samba or Central Asian dance produced a very real feeling that they had ultimately become gone team.h
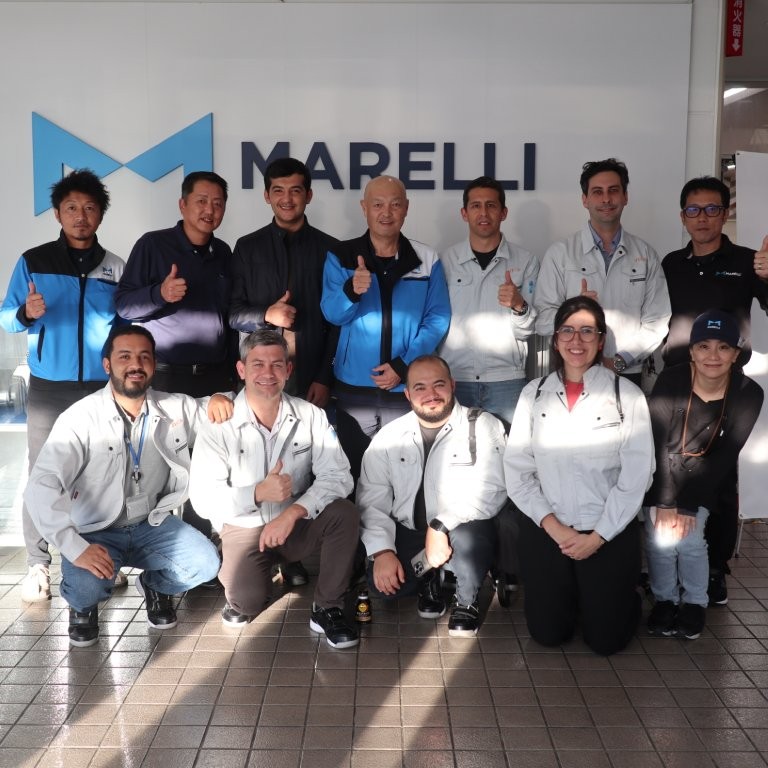
Visit to Marelli Kyushu‚ Nakatsu Plant
Although the lectures were conducted in English‚ which is not their native language‚ the participants acquired knowledge of kaizen and drew up action plans. I hope that this training will enable them to disseminate a culture of continuous kaizen culture in their workplaces and contribute to improving the competitiveness of their respective companies as a whole.